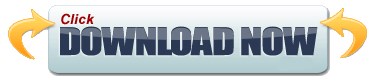
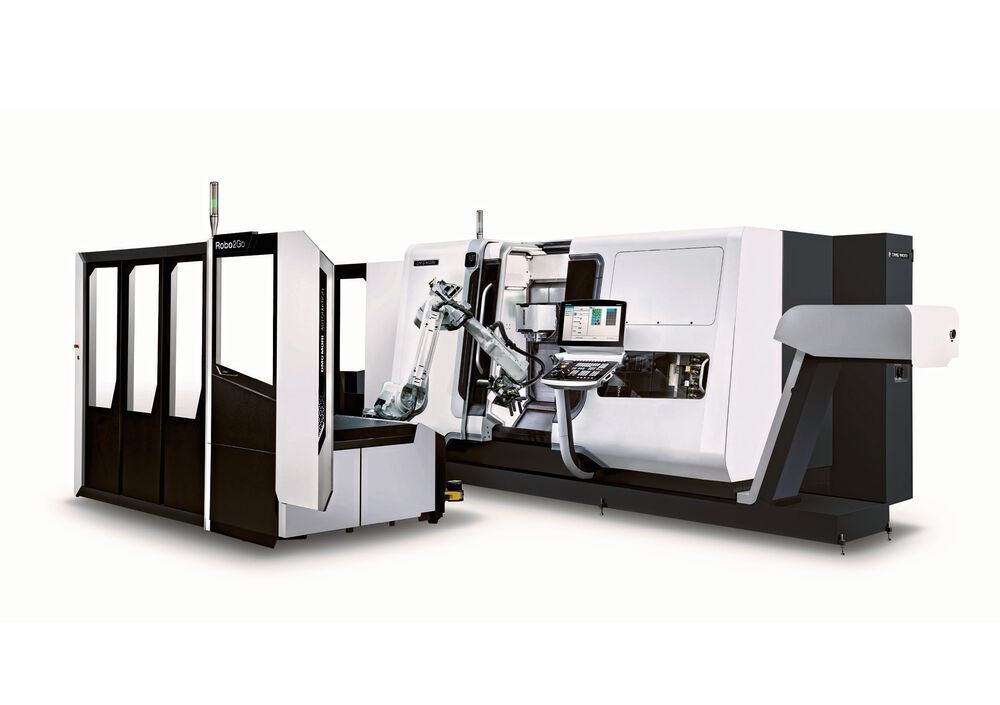

He added, "We encourage our apprentices to learn about and engage with this modern control interface and their use of advanced technology helps us to retain them at the end of their time." Dickinson observes that the younger generation of trainees intuitively understand the new control technology, as they have no preconceived ideas, which is not the case with some longer-serving machinists. “Besides being able to manufacture the standard ranges, the NTX 3000 considerably reduces the delivery times of our customised products and can cut a variety of materials, mainly aluminium required for the production of aluminium housing for higher capacity torque tools, but also alloy steels including EN24T, EN26W and EN30B in an annealed condition.”Īpprentices are introduced to the latest machine tools in the Daventry factory after their first year.

#DMG MORI MACHINE UPGRADE#
Earlier this year the latter machine was replaced by a more modern NTX 3000 7-axis multi-tasking version.Ĭhris Dickinson, Group Operations Director, responsible for all aspects of manufacturing including material sourcing, machining, assembly, testing and distribution says, "The previous NT 4250 gave us remarkable service, but we thought it prudent to upgrade to the latest model from DMG MORI, which incorporates newer technology, provides greater flexibility and is more economical to run.” The first machine tool purchases were a five-axis machining centre and N元000 lathes closely followed in 2010 by an NT 4250 turn-milling centre from DMG MORI. Key to this incredible growth is Hi-Force’s strategic decision to progress into in-house manufacturing, which meant Hi-Force ended many years of dependency on sub-contractors.

Since then, the company has witnessed ongoing success and prosperity, with almost 190 per cent growth and a tripled workforce.
#DMG MORI MACHINE PLUS#
Having everything on one huge site, spanning over 120,000 square feet, creates huge efficiency gains, for the business, plus allows our customers to see first-hand exactly how the tools, they buy and use, are manufactured, assembled, tested & certified, finished, packed and dispatched” confirms Kevin Brown, Group Managing Director. “We manufacture our products from within our headquarters and manufacturing facilities, in Daventry, where you can see the complete manufacturing process, from raw material being delivered by our steel and aluminium stock holders, to finished, boxed product being shipped out. In line with this development, Hi-Force relocated to a brand new, state-of-the-art facility in 2010, which has enabled the firm to combine all manufacturing and production facilities under one roof, alongside its sales, marketing, assembly, training, logistics and administration departments. Having previously subcontracted its component production, the company decided in 2008 to open its own machine shop and bring a majority of metal cutting in-house. In addition to offering 2,000 standard products for sale and rental, the company's engineering team based in Daventry, UK develops custom hydraulic tools to meet the needs of a multiplicity of end users. Established in 1982, Hi-Force is the UK’s leading designer, manufacturer and global supplier of hydraulic tools such as cylinders, pumps, torque wrenches, bolt tensioners, jacks, crimpers and cutters, nut splitters and flange spreaders.
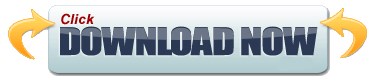